Breadcrumb
- Home
- Design and Construction Metal Molds
- Progressive Dies
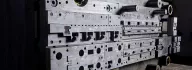
Progressive dies
At Minifaber, we design and make custom progressive dies
They are ideal for small to medium-sized parts. At Minifaber we custom-design and make them. What are their main features? What about the advantages? Let's find out together
A progressive sheet metal mold is a type of tool used to perform multiple operations on a continuous sheet metal strip as it advances through several stations, which are incorporated into the same die. It is ideal for producing small or medium-sized parts in large quantities.
In the case of a progressive die:
- The sheet metal is fed as a continuous strip from a coil, and progressively advances through the die.
- Each station performs a specific operation: shearing, bending, drawing, drilling or threading.
- The operations are synchronized, and each forward movement of the sheet metal corresponds to a complete die cycle.
Read on to explore how a progressive die works, the advantages of this type of die, and how it differs from transfer molds.
This is how a progressive die works.
Sheet metal feed: a coil of sheet metal is unwound and fed into the die.
Precise positioning: centering systems clamp the sheet and move it forward precisely.
Sequential operations: each station performs one part of the process, for example, the first one may perform pre-cutting, the second one may create holes, the third one may perform bending, and so on. The part is gradually formed as the sheet advances.
Finished part ejection: the fully fabricated part is separated from the sheet metal strip at the end of the cycle.
The advantages of a progressive die
These are the advantages that distinguish this type of metal mold.
- Efficiency: it is suitable for mass production because of its speed and continuous cycle.
- Precision: it ensures tight tolerances through accurate control over the forward movement of the sheet metal.
- Cost reduction: it combines multiple operations in a single process, reducing the need for additional fabrication.
Automation: it requires little manual handling, increasing productivity.
The differences between progressive dies and transfer molds
These are the differences between the two types, progressive and transfer molds.
- Progressive die: the sheet metal is a continuous strip that advances and is processed without being separated until the last operation.
- Transfer die: each part is processed individually and transferred from one station to another.
To summarize: when the part is medium-sized to large, the active parts of the die also become bulky, making it is necessary to create the right space between stamping stations. In this case, the transfer mold is used.
Other dies
Learn about the other types of precision metalworking dies in which Minifaber specializes.
We guarantee quality, durability and process control, while offering customized and innovative solutions.