Professional Lighting Projector
Lighting and lighting effects equipment for concerts, events and TV studios
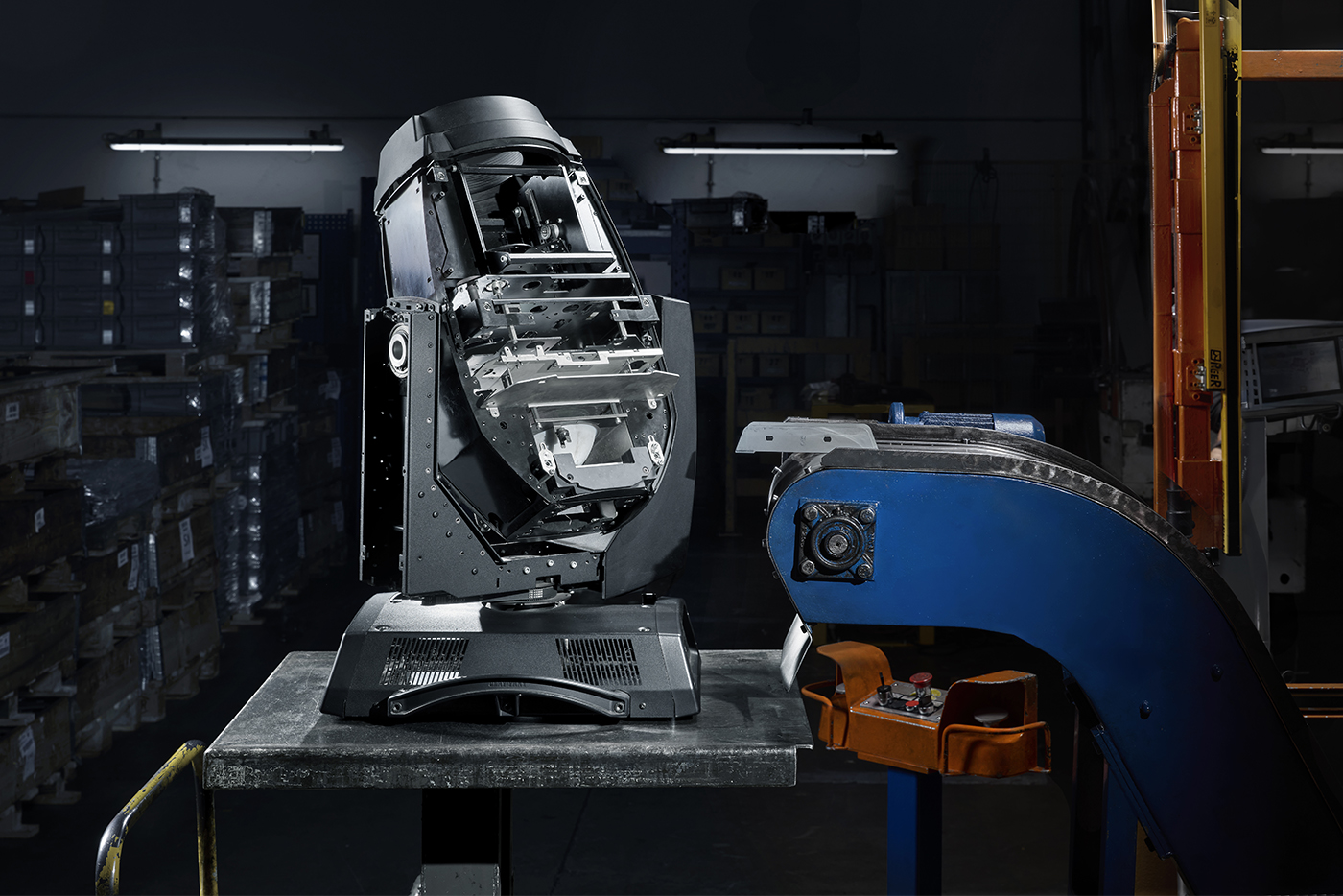
The customer first requests the manufacture of a few components for his product and then, completely satisfied with our work, delegates to us the overall production of the device, from 0 to 100.
To accomplish this, we joined forces by coordinating, in addition to in-house production departments, specialized suppliers for surface treatments, thus becoming, in effect, the prime contractors for manufacturing this complex equipment.
The implementation of this project involved overcoming several obstacles:
- the complexity of coordinating suppliers of raw materials and external surface treatments while managing their timelines to meet customer requirements
- the complexity of the geometric shapes of the product
- the need to comply with stringent regulations ensuring the safety of the product (the equipment—sophisticated and motorized—was positioned at considerable heights with safety risks)
- the need to develop vertical expertise in the field in a short period of time
- the problem of ensuring the customer a product that is resistant to the multiple stresses to which the equipment is subjected during use (high temperatures, high vibrations, and high mechanical stresses).
How did we respond to these requests?
We changed our approach from focusing on individual parts to an overall view of the assembled product.
We focused our efforts on precision, with very tight machining tolerances (laser, bending, and punching) and surface treatments appropriately done to withstand the expected thermal stresses during product use.
We have integrated several technologies, already present and active in Minifaber, to take advantage of their effectiveness.
We used special aluminum alloys, which are more difficult to machine because they are more mechanically strong but more suitable for manufacturing this product.
To succeed in all this, we dedicated an entire team of technical specialists to the project, who focused on each stage, from production to delivery of the finished projector.
The effort was rewarded by a piece of news we like to mention: these floodlights were chosen to light the opening ceremony of the 2012 London Olympic Games.
- Lead contractor with coordination of external suppliers
- Project followed from the beginning, starting from individual parts to the assembled product
- Very tight machining tolerances (laser, bending, and punching)
- Properly done surface treatments to support the thermal stresses that products must withstand
- Mix of different technologies integrated thanks to Minifaber's know-how
- Use of special aluminum alloys, which are complex to machine.