Breadcrumb
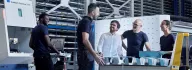
People in Minifaber
At Minifaber, our success stems from the strength of our team: a young, dynamic, and highly qualified group that combines freshness and experience to meet industry challenges with energy, creativity, and innovation.
Working with the client begins with our sales team, which collects inquiries and investigates specific needs. Next, the Project Leader team enters the scene: technical figures who assess the feasibility of the product, analyze the production cycle, and identify the most suitable technologies, leveraging Minifaber's established experience. At this stage, Project Leaders also engage with the customer to propose innovative solutions and material alternatives, improving product performance.
Teamwork involves all internal areas: technical department, research and development, time and motion, design-to-production, quality, purchasing, and the production departments, where our specific know-how resides. We also collaborate with external partners, such as suppliers, research centers, and universities, to ensure cutting-edge solutions.
The customer is supported during the sampling and prototyping stages, which are crucial for product development. This is possible thanks to our advanced technologies and Minifaber's specialized skills. The engineering department is in charge of the study of dies and tooling, while the tooling department is in charge of their construction and maintenance. The Time&Motion and Design-to-Production team optimizes the work cycle, defining the best methods in terms of efficiency, ergonomics, and tools to ensure smooth production.
Once the product goes into mass production, customer service takes over the customer’s day-to-day management, from order entry to delivery, ensuring that requests are fully met.
All other departments, such as production planning, purchasing, logistics, and production departments, are involved in the efficient realization of the product, supported by the quality team to ensure compliance with standards and the maintenance team to keep the machines running properly. Complementing our structure are teams dedicated to key functions such as administration, finance & control, information systems, health, safety & environment, and human resources, contributing to the smooth operation of the entire production process.
Training in Minifaber
At Minifaber, we believe that knowledge is the key to excel and meet our customers' needs. Every year, we invest in developing our team's skills through numerous training courses, in addition to the mandatory health and safety ones. The main topic areas that are addressed:
- quality (e.g., measuring and calibration instruments course, risk analysis and FMEA, statistical process control, certified courses to perform nondestructive testing, APQP - Advanced product quality planning & production part approval process )
- technique (e.g. mechanical drawing, materials and their use, machining, dies and die-forming, surface coatings, heat treatments, oils and lubricants, MIG GMAW and TIG GTAW welding practical training, International Welding Technologist IWT)
- information technology (e.g., Microsoft Office package, programming software of various production machinery, programming software of three-dimensional control machines, AutoCAD, machining simulation software)
languages (Italian, English, French, German)
- transversal (e.g., NLP Practitioner, Effective communication and feedback, From customer care to customer loyalty, One-on-one coaching, Emotional Intelligence, Ergonomics and posture, Safe driving, HR People Management, Corporate reporting as a tool to support strategy, The culture of diversity in the company, Management development: leadership and communication, Lean manufacturing, Time&Movement, Gemba Walk and Kaizen Week)
- administrative and regulatory (e.g., European Privacy Regulation GDPR, Master's Degree in Management Control, MOCA Disclosure - Food Contact, The Legislative Decree. 231/2001 and the Minifaber Organization and Control Model, Environmental Legislation Training, ISO Certifications).
Our in-house Academy, MLAB, offers customized training paths for each role, aligned with our corporate strategy and business goals.
Minifaber is a reality built with time and constant commitment, with a structure that allows it to provide information and support to the customer at every stage of the product life cycle. Each member of our team is a competent and indispensable resource to ensure the success of our client collaboration.