Breadcrumb
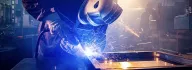
Sheet metal welding
We weld all metals using different technologies: MIG/MAG welding, TIG welding, resistance welding, projection welding, robotic MIG/MAG welding, robotic TIG welding and robotic laser welding
The expertise gained over the years and an up-to-date, multi-purpose fleet of machines means we can perform metal welding according to your specific needs.
In fact, with Minifaber, you can:
Enjoy the benefits of the most efficient sheet metal welding technologies (MIG/MAG, TIG, resistance, projection, robotic and laser)
Obtain perfect welds on sheets of different materials (ferrous materials, aluminum, stainless steel, copper, etc.).
On this page, you will see:
- Welding types
- Sheet metal welding: the materials we work with
- Minifaber: the perfect partner for sheet metal welding
1. Welding types
Our metal welding service is open to those who want to produce small batches, as well as those who need to produce large quantities of welded sheet metal.
MIG/MAG welding
MIG/MAG welding is a continuous wire welding process in which an inert (MIG) or active (MAG) gas protects the weld pool. MIG/MAG welding is used where high productivity and high application flexibility are required. Explore the advantages of MIG/MAG welding.
TIG welding
TIG welding is one of the most popular ways to weld sheet metal, as it provides high-quality standard components. It is particularly suitable for welding thin parts, and can be used for both continuous and spot welding, especially on stainless steel. Click here to learn more about this type of welding.
Resistance welding
Resistance welding is a metal welding technique in which material is melted by means of electrical resistance. Generally used to weld ferrous materials and stainless steel, resistance welding ensures high standards together with low cost. Visit the dedicated in-depth page to explore resistance welding.
Projection welding
Projection welding is a resistance welding technique that involves placing bosses on the metal to be welded. During the sheet metal welding process, the welding current is concentrated on the boss, which melts to obtain a weld in a short time, with final results that ensure excellent quality at low cost. Click here to explore projection welding.
Robotic TIG, MIG and MAG welding
Robotic welding is performed by programmable industrial robots. Used mostly in situations where welding repetition is required, it provides repeatable precision that is difficult to achieve with manual welding. Click here to learn more about robotic welding.
Laser welding
Laser welding can weld metals and metal alloys to achieve thin and deep sheet metal welding with little or no part deformation due to the low heat input. It can be performed on all weldable materials. Click here to explore laser welding.
2. Sheet metal welding: the metals we work with
We can apply the aforementioned processes to a wide range of different metals to obtain semi-finished or finished products. Using these processes, we perform sheet metal welding on ferrous materials, aluminum, stainless steel, and copper.
Ferrous material welding
Given the widespread use of this material in various sectors, iron welding is one of the most in-demand. Thanks to the skills we have acquired over the years, we can weld ferrous materials with the highest precision to achieve an extremely accurate result. Learn more about how ferrous material welding is done in Minifaber.
Aluminum welding
Known for its malleability, light weight, low temperature resistance and corrosion resistance, aluminum is used in any sector that needs these properties (electromechanical, medical and aerospace). We specialize in MIG/MAG welding on aluminum, TIG welding on aluminum and any other aluminum welding process required by customers. Learn more about aluminum welding.
Stainless steel welding
Stainless steel is a special alloy that has important attributes such as corrosion resistance and high hygiene standards, which is why it is widely in demand for the food and medical sectors. For more than 65 years, Minifaber has been welding stainless steel according to each specific request. Click here to learn more about stainless steel welding.
Copper welding
Copper is used in the electrical and electromechanical fields because of its high electrical and thermal conductivity, and its malleability. We also perform copper welding to serve all our domestic and international customers. Click here to explore copper welding.
Minifaber: the perfect partner for sheet metal welding
For more than 65 years, Minifaber has been involved in cold metalworking and sheet metal welding, proving to be the perfect partner in projects that require a high level of accuracy, reliability and technological advancement.
Choose Minifaber's sheet metal welding service, and a dedicated team will listen and provide proactive solutions.
Our technical advice includes:
An interview with our experts to understand the technical characteristics of the sheet metal welding project that the customer intends to implement
A feasibility study to achieve the highest quality while reducing waste
Careful selection of consumables and the best welding technique to be used to meet the customer's production requirements
Project implementation based on a large fleet of technologically advanced machines
Attentive quality control to ensure that the end product meets all the specifications defined at the initial consultancy stage.
Minifaber, professional sheet metal welding services for small and large quantities
Contact us without obligation for more information
Metal welding
We can apply the aforementioned processes to a wide range of different metals to obtain semi-finished or finished products.
Using these processes, we perform sheet metal welding on ferrous materials, aluminum, stainless steel, and copper.