Breadcrumb
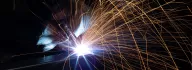
MIG/MAG welding: we explain what it is, how it works, and what advantages it offers
The MIG/MAG welding process is one of the most popular, and is suitable for handling very high production rates. This is how MIG/MAG welding works and what its advantages are.
Here is what you will learn on this page:
MIG/MAG welding: what is it all about?
The difference between MIG and MAG
The advantages of MIG/MAG welding
How the process is done in Minifaber.
What does MIG/MAG welding mean?
MIG/MAG welding is an electric arc welding process with continuous wire in which the metal is under a gas shield (GMAW, or Gas Metal Arc Welding).
What does it mean? Let’s analyze all the elements of the definition:
MIG/MAG welding is a type of electric arc welding. To melt the metals and enable welding, it harnesses the power emitted by an electric arc that strikes between the electrode (the filler metal itself in this process) and the metal to be welded.
The filler metal consists of a metal wire, generally supplied in coils, which pulled into the welding torch by a motorized roller system, and from there pushed into the weld pool. From a metallurgical aspect, the filler metal serves to improve the weldability of the material and minimize the welding defects that may arise, such as cracks and porosity. The filler metal also has the function of filling the weld gap, typically on the edges of the metal sheets to be joined. In this way, the molten material connects the metal sheets to be joined.
Another key element in this process is the action of the gas. How? To shield the weld pool, improve weldability, and prevent oxidation, cracking and other defects. The gas generally comes from a cylinder and is fed directly into the welding torch to surround the wire that will melt in the pool.
MIG/MAG welding: the difference
To understand the difference between MIG and MAG welding, it is sufficient to understand the meanings of their names:
MIG stands for Metal Inert Gas, i.e. metal welding under an inert gas
MAG stands for Metal Active Gas, i.e. metal welding under an active gas.
Thus: MIG welding uses an inert shielding gas, while MAG welding uses an active shielding gas. Inert gases mainly serve to shield the molten pool, while active gases, in addition to shielding, also help to improve the molten pool penetration. The most commonly used gas in MIG welding is argon, while argon and carbon dioxide mixtures are used in MAG welding.
The choice between MIG and MAG is dictated by multiple factors such as the type and thickness of the material to be welded, the joint type, and the specifications required by the project.
The advantages of MIG/MAG welding
MIG/MAG welding offers fast welding speeds, large amounts of material filling, and can be either manual or robotic. The sources and equipment for this process are relatively cheap and more readily available than for other processes. All these reasons make MIG/MAG welding the most popular, accessible, and economical process.
The MIG/MAG process has evolved significantly in recent times. Specific processes have emerged that can weld not only very thick but also thinner material. Penetration has improved, and the defects typical of this process have been reduced, such as the large amount of molten metal spatter, and the large heat input that tends to deform welded sheet metal.
MIG/MAG welding in Minifaber
At Minifaber, we are equipped to weld metals with MIG/MAG processes: we can weld sheet metal of different thicknesses and of almost all materials (ferrous materials, aluminum, stainless steel) for applications in the most diverse sectors (electromechanical, vending, gas distribution, EV charger and welded structures in general).
Our welding service is suitable for fabricating both small and large quantities, and applies to semi-finished and complex finished products. We perform each stage in-house, within the company, so you have a firsthand guarantee of quality control, lower costs and faster turnaround.
All this is made possible by our technicians, who posses up-to-date skills and the necessary license to perform quality work safely, and our fleet of machines:
5 anthropomorphic robots with workpiece positioning systems on rotary tables
12 manual welding machines.
Minifaber, professional MIG/MAG welding services for small and large quantities
Contact us without obligation for more information
Metal welding
We can apply the aforementioned processes to a wide range of different metals to obtain semi-finished or finished products.
Using these processes, we perform sheet metal welding on ferrous materials, aluminum, stainless steel, and copper.