Breadcrumb
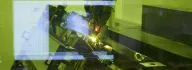
Laser welding: what it is, its advantages and all the types
Because of its ability to bring a very high energy density in a very small and concentrated space, laser technology is used in the laser welding process to melt the metal and make high-penetration welds, while minimizing heat input and material deformation.
On this page:
- What laser welding consists of
- The advantages of laser welding
- Laser welding types
- Heat conduction laser welding
- Deep laser welding
- Other welding types
- Laser welding in Minifaber
What does laser welding consist of?
It is a process that allows metals to be welded by a beam of light (photons) focused on the specific spot where they are to be joined. The laser beam concentrates all its power in a very narrow spot called the focus, and the laser beam energy on the metal increases the kinetic energy of the atoms until the material reaches its melting point.
The laser process can be applied to both higher and lower thicknesses, and ensures maximum execution speed due to the physical atomic characteristics of the laser beam.
The advantages of laser welding
Laser welding is a precision welding technique that does not create molten metal spatter, and has other advantages that make it particularly effective and successful compared to other processes:
Minimum heat input, which means the metal is not deformed;
Optimum aesthetics of the weld, which is clean and free of molten metal spatter
Manageable penetration depth, depending on the characteristics of the required joint;
High processing speed, which reduces not only time but also cost.
Laser welding types
Depending on the usable parameters, laser welding is then divided into heat induction welding and deep (keyhole) welding.
Heat conduction laser welding
With heat conduction laser welding, heat propagates through the metal as it does with other electric arc welding processes, and some other processes. This process is used as a second weld pass to make weld seams more aesthetically pleasing, wider and shallower, and to seal tanks, gas leaks and fluid leaks in general.
Deep laser (keyhole) welding
Keyhole welding is used to perform deep penetration welding, and the seam is narrower than in conduction welding.
During this process, the laser generates a hole of varying depth, depending on the laser power and other parameters. In this hole, the material melts and then vaporizes, allowing the laser beam to go even deeper.
The pressure created inside the hole keeps it open. The hole formed by the molten metal collapses inward when the pressure decreases, forming the weld seam. Seams made with keyhole welding are narrow and deep, so they are often combined with a second pass of conduction welding.
Laser source types
There are different laser beam sources.
The most important and the ones used in Minifaber are CO2 source and solid-state source. Each has its specific field of application.
Laser welding in Minifaber
Minifaber specializes in “custom” metalworking, and has been committed to meeting the demands of its customers for more than 65 years.
Our technicians sit down with you to study your project together and find the best process to implement it.
Among the various existing welding techniques, Minifaber also exploits laser welding, which is done using state-of-the-art technological machinery with the utmost respect for safety. The ultimate goal is to produce for you finished or semi-finished products that are precise and clean, and perfectly meet the desired result.
If you would like to rely on Minifaber's experience for a laser welding service, contact us now, and we will be happy to assist you with any of your requests.
Minifaber, professional laser welding services for small and large quantities
Contact us without obligation for more information
Metal welding
We can apply the aforementioned processes to a wide range of different metals to obtain semi-finished or finished products.
Using these processes, we perform sheet metal welding on ferrous materials, aluminum, stainless steel, and copper.