Breadcrumb
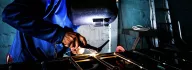
The aluminum welding process
How is aluminum welding done? How many types of aluminum welding are there? For what applications? Let's learn more about the welding and services provided by Minifaber.
Aluminum is one of the most widely used materials across all sectors: it is light but strong, has good corrosion resistance and high stiffness. It has high impact resistance at low temperatures (cryogenic applications) and good malleability.
Aluminum welding, however, requires precise attention; this knowledge is essential when welding aluminum.
What you need to know before welding aluminum
First, not all aluminum alloys are weldable. Therefore, it is necessary to know the material before taking on welding.
Then, aluminum is coated with a hard, corrosion-resistant natural oxide layer called alumina. If flakes of alumina get into the weld pool, they will go on to create cracks, porosity and other defects, so it must be prevented from happening by removing the alumina layer with mechanical brushing, pre-heating or other techniques that Minifaber knows well.
Aluminum welding: MIG/MAG or TIG?
Both processes can be used to weld aluminum. Which one to choose depends on the thickness of the aluminum and the preparation of the edges to be welded.
For low thicknesses, TIG (Tungsten Inert Gas) welding, which exploits an infusible tungsten electrode and an inert gas shield, is excellent. In addition, the alumina oxide is destroyed in alternating current mode, ensuring a good weld. The use of filler material is always recommended to improve the weldability of the base metal.
MIG/MAG welding is more suitable for higher thicknesses and for filling gaps with an appropriate filler material that prevents the formation of cracks or porosity.
Aluminum welding: laser = speed
When choosing from the various aluminum welding techniques, the required production speed must also be considered. Laser welding is most suitable when the time it takes to weld a part must be reduced: not just fast, but also accurate and safe, aluminum laser welding requires the foresight to prepare the edges thoroughly for welding to remove the alumina layer, and use a suitable filler material to improve the weldability of the material.
With Minifaber, you can choose from a variety of aluminum welding techniques
At Minifaber, we have the right skills and machinery to perform all three of the aluminum welding techniques we have discussed: TIG and MIG/MAG welding (both manually and with robotic systems) and laser welding with 3D robots. Depending on the types of the parts to be fabricated, our technicians always know how to choose the right technology to optimize resources and give you flawless results.
Minifaber, professional aluminum welding services for small and large quantities
Contact us without obligation for more information
Metal welding
We can apply the aforementioned processes to a wide range of different metals to obtain semi-finished or finished products.
Using these processes, we perform sheet metal welding on ferrous materials, aluminum, stainless steel, and copper.