Breadcrumb
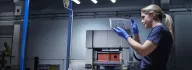
High-tech sheet metal shearing
Metal shearing can shape any sheet metal using punches and dies to cut it and give it the desired shape.
The sheet metal shearing process requires great experience and maximum precision.
Minifaber specializes in sheet metal fabrication, and has the know-how, technologies and flexibility to perform shearing on iron, stainless steel, aluminum, copper and special alloys. Minifaber's great advantage is the use of technologically advanced machinery that can perform sheet metal shearing accurately and quickly.
Key advantages of shearing
Below is a list of the key advantages of the metal blanking process (ferrous materials, stainless steel, aluminum, copper, brass, special alloys).
1. High precision
Shearing results in parts with very tight dimensional tolerances and well-defined profiles. It is ideal for making complex components with precise details.
2. High production speed
It is a fast process, especially when automated machinery is used. It is suitable for mass production, with short cycle times per part.
3. Low material waste
Optimizing part layout on the sheet metal (nesting) minimizes scrap, thus increasing economic and environmental efficiency.
4. Versatility
It can be used on a wide range of materials, such as steel, aluminum, copper, brass, and light alloys. It is suitable for different sheet metal thicknesses, from thin to thicker.
5. Repeatability and uniformity
Each sheared part has the same dimensions and quality, ensuring high uniformity in production batches.
6. Compatibility with other processes
Shearing can be combined with other processes (e.g, bending, drawing) in a single progressive die to create finished parts.
7. Economic efficiency for large volumes
Once the die has been made, the unit cost of parts decreases significantly as production increases.
8. Design flexibility
It can be used to make parts with very different and complex geometries, depending on the needs of the project.
9. High-quality finish
The cut surface is generally clean and precise, reducing or eliminating the need for additional work.
10. Low environmental impact
The process does not require heating (as in hot processing), reducing energy consumption and emissions.
We at Minifaber have extensive know-how in this sheet metal process and support our customers daily in producing finished and semi-finished parts with excellent results.
Minifaber, professional metal shearing services for small and large quantities
Contact us without obligation for more information
Metal shearing
Thanks to its experience and knowledge, Minifaber can perform shearing on all types of metal, working sheet metal of different thicknesses to make a wide variety of shapes. In addition to the most common metals, our fabrication processes are flexible enough to also perform shearing on brass and other special alloys.
Minifaber, 65 years of shearing know-how for small and large quantities.
Contact us for a quote and feasibility study
COMPLETED PROJECTS
Coffee machine
The client involved us in the creation of a series of coffee machines for the Ho.Re.Ca. market that differs from those you can buy in stores: construction characteristics, aesthetics, durability, and materials are superior to the consumer market.
Minifaber takes over the co-designing of metal parts, to be designed for production through dies.
Additional challenge: the really tight time frame for implementation.