Breadcrumb
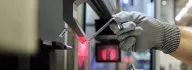
The custom sheet metal bending process in Minifaber
When we talk about custom sheet metal bending to the customer's drawing, we refer to a cold deformation process that exploits the ability of a press brake to deform sheet metal to obtain special, tailored bends from a flat geometry.
On this page, you will learn about:
How Minifaber implements the bending process
Elements to consider for sheet metal bending
Technical material
Procedures
Safety protocols
Metals
Choose Minifaber to implement your project.
Minifaber is an established leader in the cold metalworking sector. Sheet metal bending is part of our core business, and we have always experimented with new technologies to achieve the “custom” shapes required by customers.
In this process, pressure and tooling are two key elements in obtaining bent products from flat sheets. We can bend any metal chosen by the customer, as long as it has the property that makes it capable of being bent: its plastic reserve.
How Minifaber implements the bending process
Custom sheet metal bending is a process to which we dedicate a specialized department in Minifaber.
We start with the understanding that every project is different and that customers have specific needs.
For this reason, we place dialog with the customer at the center of the entire process, because it is essential to fully understand what the customer's needs are and to study the best process to achieve its goals.
At Minifaber, you will find not only the know-how of our professionals, but also attentive and participative listening that will result in beneficial co-design to achieve the best results for you and your company. You will also be able to choose from machinery and tooling to ensure successful fabrication, which we will carry out with innovative processes to produce a precise product with a quick turnaround.
Elements to consider for sheet metal bending
Before bending sheet metal to a drawing, it is essential to consider a number of factors that are critical to the success of the process.
Technical material
It involves assessing the fleet of machines and tooling available, the technical specifications of each individual press, quality control tools, and the experience of our technicians. We refer to our long, proven experience and knowledge of the characteristics of our tooling and the metal materials with which we work.
It is only by assessing all these aspects that we can make an objective, systematic feasibility analysis and implement what our clients require in the best way.
Procedures
In this case, we carefully assess which press brake and tooling best suits the customer's fabrication needs, and thus achieve fully customized fabrication.
To obtain an end product that meets the initial requirements, it is therefore essential to set the press parameters correctly and then choose the tooling from the many options available in Minifaber before proceeding with the bending.
Currently, Minifaber has 7 automated presses at its disposal, thanks to a computer numerical control system, the CNC.
Safety protocols
All automated machines currently in Minifaber feature advanced safety systems to prevent accidents.
Nonetheless, we take additional measures to protect operators, such as ongoing technical and accident-prevention training, and we provide a series of studies and interventions to prevent hazardous situations. To ensure that the presses work perfectly and avoid production downtime, we monitor and maintain the machinery constantly.
In addition, carrying out such checks periodically will keep the machines “healthy”, as well as ensure that custom sheet metal bending is more accurate and faster, while preventing unexpected machine downtime.
Metals
The custom sheet metal bending offered by Minifaber is “tailor-made” because, in addition to defining the shape together with the customer, the customer can choose the material to be worked.
These are the materials we work with:
Aluminum: a malleable, light material, perfect for making semi-finished products. It is suitable for a variety of sectors, such as electromechanical, electromedical, lighting, EV charger, home appliance and more;
Stainless steel: stainless steel is used in the food, electromedical and household appliance sectors, and more. Highly aesthetic requirements are often required, so the sheet metal must be handled with care and experience, choosing the right tools and film-protected materials;
Ferrous materials: these materials are widely used, including electrolytically and heat-coated variants. Because of this, they are suitable for a wide variety of application areas;
- Copper: the electromechanical and EV charger sectors require sheet copper bending as it is a material with high electrical and thermal conductivity, combined with malleability.
Choose Minifaber's custom sheet metal bending service
Thanks to Minifaber, your sheet metal bending project will be precise, fast, and customized. By choosing the expertise of a leading cold metalworking company, you will be able to engage with a team of experts who will listen to your requirements and analyze your project.
At Minifaber, we enhance your ideas and your business because:
We are proactive and believe in the power of dialog
We are flexible, competent and have long experience
We believe in the value of research and innovation
We believe in the power of training and continuous learning
W want to offer you the best possible product through advanced techniques and machinery.
Minifaber, professional custom sheet metal bending services for small and large quantities
Contact us without obligation for more information
Metal bending
Metal bending is one of the specialties of Minifaber, experts in cold metalworking since 1960. Learn more below about some types of sheet metal bending and the characteristics of this process with metals such as aluminum, stainless steel, copper, and ferrous materials.