Breadcrumb
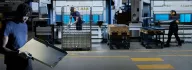
The metal bending process in Minifaber
Minifaber has more than a decade of experience in bending steel, aluminum, copper, and other metals for a variety of industries: from electromechanical to medical and kitchen robotics such as ice cream machines. Metal bending is a cold working process that makes bends in sheet metal as required by the customer's drawing. This is how it is actually done in Minifaber.
Metal bending requires the use of a bending or paneling machine, and can produce panels or bent sheets from flat semi-finished products.
Minifaber owns as many as seven brake presses and one paneling machine. These are technologically advanced, state-of-the-art, programmable CNC machines that can bend the following with the highest precision:
- Aluminum and its alloys
- Stainless steel
- Ferrous materials
- Copper and its alloys.
The press brake
Bending a metal with a press brake is one of the most precise, simple and inexpensive ways to make prototypes and batches, even in very small runs: a blade pushes the sheet metal into a V-die, which forms the bend in the part.
There are three different types of metal bending:
Air bending - the sheet metal is placed on two supports and deformed by the punch, which does not reach the bottom of the V-die; this manages the natural springback of the material
Coining - as in air bending, the sheet metal is placed on two supports, but in this case the punch, or blade, reaches the bottom of the V-die; in this case the bend angle is repeatable on all parts produced
Hemming - this serves to eliminate sharp edges on the part by creating a radiused double thickness on the sheet metal.
The use of programmable brake presses makes it possible to manage the inevitable springback after bending, the magnitude of which depends on the nature of the metal, its hardness and its elasticity.
The paneling machine
Bending metal using a paneling machine is ideal for parts that need to be bent on all four corners, with complex bends that differ from each other.
In this case, the sheet metal is placed on a worktable, and the blank holder on the machine clamps it while a tool bends it.
Minifaber's metal bending service starts with a thorough analysis of the project together with the customer. Once we understand the specific requirements and final application of the part, we proceed with sheet metal bending, outlining the best strategy to achieve a flawless result. This also involves identifying the most suitable machine to achieve the objective.
The sectors we work for
We offer a metal bending service for a wide variety of sectors, including:
Electromechanical
Home appliances and kitchen robotics
Vending
Professional lighting
Medical
EV charger
Gas distribution.
Metal bending and more
Metal bending is just one of the services we provide at Minifaber. In fact, since 1960, we have been specializing in cold metalworking, such as:
Shearing
Drawing
Sheet metal hydroforming
Punching
making step die and transfer mold parts
2D and 3D laser cutting
welding: Laser-MIG/MAG-CMT-TIG-Resistance-Capacitor Discharge
Metal component assembly
Surface coatings and heat treatments of the metal parts we fabricate.
Minifaber, professional sheet metal bending services for small and large quantities
Contact us without obligation for more information
Metal bending
Metal bending is one of the specialties of Minifaber, experts in cold metalworking since 1960. Learn more below about some types of sheet metal bending and the characteristics of this process with metals such as aluminum, stainless steel, copper, and ferrous materials.
Minifaber, 65 years of cold metalworking know-how for small and large quantities.
Contact us for a quote and feasibility study
COMPLETED PROJECTS
Sterilizer
The client was looking for a partner who could assist him in the realization of this complex product.
Special care had to be taken in manufacturing the deep-drawn part as it had to meet the technical requirements for pressure vessels with PED and ASME (American) certifications.