Breadcrumb
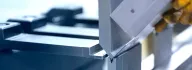
The metal bending process in Minifaber
They are used in sectors such as electromechanical, gas distribution, EV charger, home appliance, and to make semi-finished parts and everyday items. Minifaber is able to process ferrous materials (including coated), at low cost: among many processes is bending, in which flat sheet metal can be transformed into semi-finished parts of different shapes.
Let's see specifically:
How ferrous material bending is done
What machinery is needed
The advantages of cold bending.
How ferrous material bending is done
Ferrous materials lend themselves very well to cold deformation and thus bending. Of course, as the thickness increases, so do the fabrication difficulties (that is why it is important to rely on industry specialists such as Minifaber). Bending metals, and particularly ferrous metals, is a cold fabrication process that involves plastic deformation of sheet metal. It can transform sheet metal into the complex geometric shapes required by the customer's drawing. Bending ferrous materials results in permanent deformation due to bending stress, or sometimes rotational stress, until the desired shape is achieved.
For ferrous materials to be bent, they must be subjected to a type of pressure, which must overcome the elastic limit of the material in order to obtain permanent deformation: bending. Once bent, the natural springback of the material must be considered in order to adapt the bending parameters to compensate for it.
What machinery is needed for bending
The ferrous material bending process is done by press brakes. The blade movement is set according to the bend length and bend angle.
If a very small bend radius is required, the blade, V-die and sheet metal to be worked must come into contact with each other: the so-called coining bend. In this case, Minifaber technicians prudently check that the small bend radius is not going to create cracks and breaks.
On the contrary: if a wider bend radius is required, the blade and V-die do not come into contact: the so-called air bend. Minifaber is an expert in making semi-finished products from ferrous materials, exploiting a fleet of innovative machines and the ability to meticulously interpret customer requirements.
The advantages of cold bending ferrous materials
Bending ferrous materials (including coated), serves to make all kinds of semi-finished products. Cold bending results in a permanent bend in the sheet metal. It is important to know the physical and mechanical properties of the material to be worked.
The advantages of cold bending are:
Low fabrication cost;
Tooling versatility;
Immediate availability of V-dies and blades, Minifaber has a large fleet of tooling
- Lower possibility of error, thanks to our expert personnel.
Minifaber, professional ferrous material bending services for small and large quantities
Contact us without obligation for more information
Metal bending
Metal bending is one of the specialties of Minifaber, experts in cold metalworking since 1960. Learn more below about some types of sheet metal bending and the characteristics of this process with metals such as aluminum, stainless steel, copper, and ferrous materials.