Breadcrumb
- Home
- Design and Construction
- Design and Construction of Molds For Sheet Metal
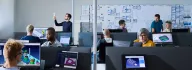
Design and construction of molds for sheet metal
We design and manufacture sheet metal molds for cold metalworking in-house
Design and construction of molds for sheet meta: Minifaber’s experience
Minifaber designs and constructs molds for cold sheet metal fabrication, offering custom solutions to meet customers' most complex needs.
Thanks to established experience, a highly specialized Engineering Department and fleet of advanced machines, we are able to make dies that meet the highest quality standards and satisfy specific requirements, such as precision, efficiency and waste reduction
We use leading-edge computer systems for simulation and design to ensure maximum accuracy at every stage of the process. All our dies meet international quality and certification guidelines.
On this page we will explore the steps of making a die and the types of die:
- How we design your die
- The die-making stage
- Working on the dies made
- The different types of die available
- Choose Minifaber to make your dies
Die design
When a customer submits its request for a die design to us, our engineering and design personnel meet to understand its needs and offer guidance on where optimizations can be made. This leads to a finished product that meets even the most complex requirements.
For die design, we often do “finite element analysis” using dedicated software to analyze the method and feasibility for design validation.
The finite elements methods offers very reliable true virtual die testing in order to avoid time-consuming and costly tests on trial or final dies.
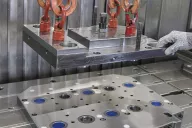
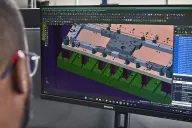
Die making
Our sheet metal molds are designed and manufactured to ensure the best finished and semi-finished products.
With a view to waste minimization and production precision, our team uses computer systems capable of interfacing and dialogging with the most modern operating systems.
Engineering/design personnel use them for production and drawing verification as early as the design stage and again later at the die-making stage.
Our high level of expertise in die making and the complete fleet of machines enable us to design and construct all kinds of sheet metal mold: blanking dies, drawing molds, progressive dies, transfer molds, hydroforming dies.
Are you looking for a qualified sheet metal mold design and construction service?
Contact us without obligation for more information
Die making
To ensure an optimal die-making service, Minifaber uses a technologically advanced fleet of machines. Our machines are constantly upgraded and represent Minifaber's ongoing commitment to providing its customers with an excellent die-making service.
Minifaber can not only make sheet metal molds, but can also carry out maintenance with the ultimate goal of keeping them in their original working condition.
Types of die
We design and make the following dies for metal materials and sheet metal:
- Progressive dies (including with built-in thread cutters) to produce components in large quantities and at high rates. The finished product can be made in a succession of steps using the same die, achieving better results in terms of product quality, production speed and low cost.
- Transfer molds, to make the finished product in a succession of passes over a series of mold using a transfer system to transfer the part from one station to another. Compared with progressive dies, they offer more freedom to work on deeper and taller deep-drawn parts.
- Drawing molds, which make it possible to obtain metal components and finished products with deep geometries in circular, rectangular or irregular shapes. In demand in every sector, our drawing molds guarantee maximum precision and long-term efficiency.
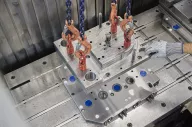
Choose Minifaber to make your dies
For over 65 years, we at Minifaber have been stamping and cold working metals. We do this with a high level of innovation, focusing on flexibility and attentive customer service.
Through co-design, we align ourselves with customers' requirements and assist them in designing and choosing the most suitable materials and shapes for manufacturing.
Each die is carefully custom-made thanks to the know-how of our experts and our large fleet of machines. Our machines are automated so that precision stamping is performed efficiently and quickly, increasing productivity and decreasing waste.
When you involve Minifaber, you will be talking to an expert in the field of cold metalworking, and you will experience firsthand the care our technicians put into each and every project.
Minifaber, 65 years of cold metalworking know-how for small and large quantities.
Contact us for a quote and feasibility study
Our state-of-the-art machines for design and construction of molds for sheet metal
Minifaber has a fleet of state-of-the-art machines dedicated to design and construction of molds for sheet metal, with advanced technologies that ensure precision and reliability. These include wire and die-sinking EDM machines, 3- and 5-axis machining centers, CNC lathes, and grinding machines, capable of complex, high-precision fabrication.
The process is supported by a heat treatment furnace, a die opening press, and an automated warehouse for components and spare parts. In addition, we use a three-dimensional measuring machine to check the machined parts, ensuring the highest precision at every stage.
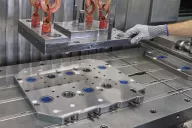