Breadcrumb
The art of sheet metal bending
Although the sheet metal bending could seem you extremely simple, it hides a series of rules and tricks that allows you to realize simple or extremely complex geometries.
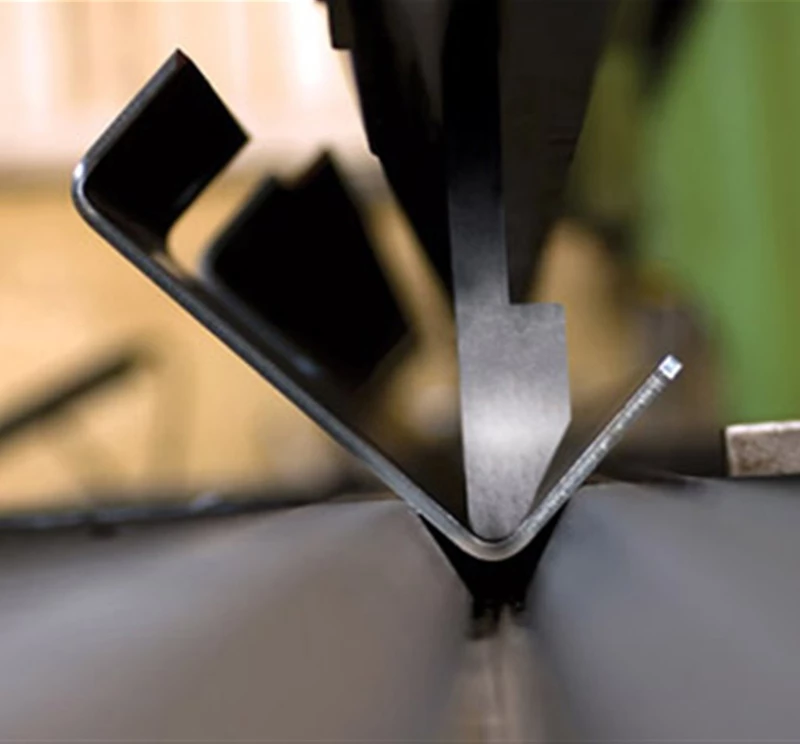
The sheet metal bending is one of the most common use process in manufacturing industry.
Similar to the forming process, the bending works creating a change of direction in the geometry of the sheet metal, for example, transforming a flat sheet metal in a angular sheet. In fact, through the use of a CNC press and a mould, the sheet metal can reach the shape of a corner.
A process that allows you to realize simple or extremely complex geometries and which can be applied on a wide range of metals: from iron to copper, from brass to aluminum, stainless steel and other special alloys.
- How does the sheet metal bending work?
In the sheet metal bending, a piece of metal is located between two dies: a punch and a die. The first one applies a force on the sheet metal pushing it down until it’s match up with the mold below.
There’re a great variety of press brake tools in order to obtain different metal bending; for example, if you need to realize angles greater than 90°, you’ll require specific tools which work by applying an horizontal pressing force.
When you need to decide the kind of bending, you must take into account: the thickness of the metal, the type of curve you want to obtain, the angle of bend, its size and others.
A general rule about this last topic (the size of dies) could be: larger is the bending you want to process and less acute must be your upper and lower mould.
- Which are the most common sheet metal bending processes?
Concerning issues that we have just mentioned, you can choose among different types of bending.
The sheet metal bending with V-die or air bending – probably the most common when the need is to reach corner till 90°, it’s realized with just two tools: an upper mould (punch) and a lower one (the die) and a sheet metal located between them. Then there’s the U bending, the edge bending with wiping die – this kind of process uses cylinder mould– and the rotary bending.
Factors that affect the sheet metal bending
There are many factors that can affect the result of sheet metal bending. For example, the most important are:
- The metal properties
- The stress caused from the previous process
- The kind of the edges you want realize
- The length and the thickness of the work piece
- The processing temperature