Breadcrumb
Sheet metal stamping, how a progressive die stamping works
Sheet metal forming is a process where parts are made for a wide range of uses. Sheet metal in this process refers to a piece of metal which takes shape thanks to stamping processes.
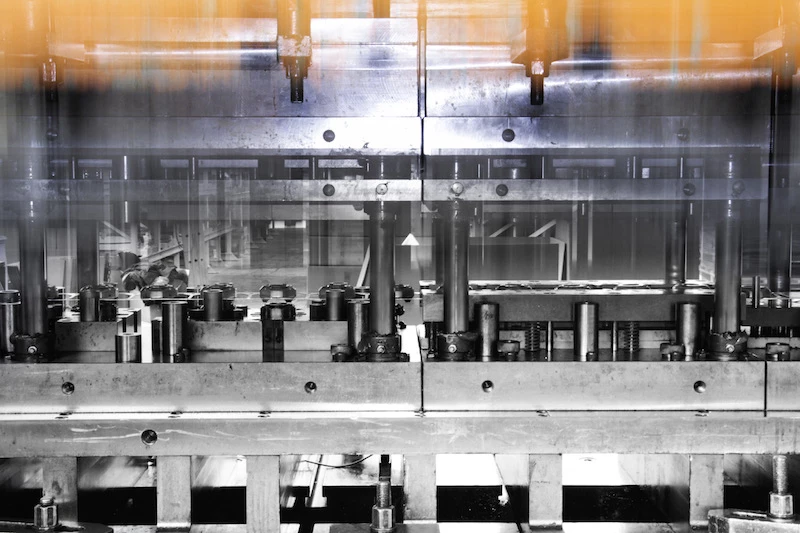
There is a distinction between a sheet metal and plate metal, with the former coming with a thickness which a quarter inch or more while the later has a thickness of more than a quarter inch.
Also when it comes to application the two parts have varied used. Sheet metal is mostly used in the making of cars, aircraft, furniture, computers, farm equipment among other used.
Sheet metal stamping is divided into three main classes; the cutting class where shearing forces are used to remove material, although at times this is not regarded as metal forming process the fact remains that it is has great importance in industrial operations.
The second class is bending where the sheet metal is formed about the axis. Deep drawing involves forming a box or cup with a base which is flat, straight walls or inclined.
Other processes include progressive die stamping, spinning forming among other things. After knowing what sheet metal forming is all about, now let’s get to specifics, through discussing a process which has led to formation of products which are durable and effective in serving their purposes.
Progressive die stamping is a series of metal forming where the final product comes in two or more orderly operations. It involves feeding the coil through the station, then piercing and forming the preceding stations. The last station involves blanking and discharging the skeleton.
The complexity, the size and the volume of the whole process determine production of any part in the progressive die. In such a case the process come in handy in the production of the large volume of parts as well as keeping the cost to the lowest point. Reality dictates that the standards ought to be high and at the same time precision and durability need to be among the highest factors considered in the process.
The nature of the progressive dies coupled with the complexity demands that all factors, which play some part in achievement of the expected results in terms of quality, blank position and boundaries as well as pilots, need to be addressed.
Pilots are known to play a very crucial role in the progressive die, they are meant to fix the strip in the right position and at the same time maintain the necessary control over it. Additionally they come in handy when considering the essential positioning in the tool closing and operations in the progressive transfer dies.
There are other factors which need to be considered in the process to make it yield the desired results. Timing must be right, there ought to an interaction of the carrier, upper and low tools as well as the pads.
Progressive die stamping has several benefits, they include increased productivity as well as the significant reduction on the cost.