Breadcrumb
Sheet metal stamping design: give shape to your ideas
Do you have an idea in mind, but have no idea how to give it shape? You've come to the right place. Minifaber has decades of experience in the design and manufacture of sheet metal molds.
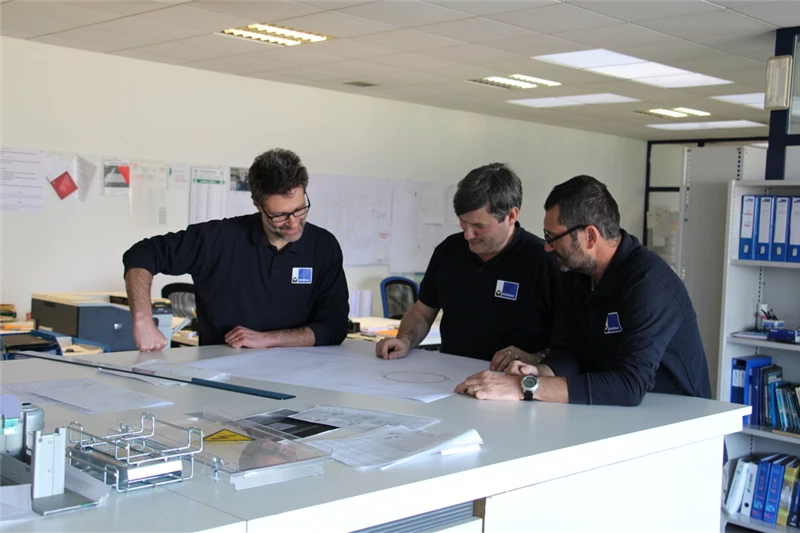
Unfortunately, great design ideas are often left on the back burner since the skills to transform the design into reality are lacking. Complex processes and demands for the finished product can be frightening. Minifaber, on the other hand, thanks to its sheet metal stamping design skills, is able to carry out complex processes on both semi-finished and fully assembled products.
Once the idea is submitted to us, our specialized technicians sit together with the customer and provide their preparation and expertise to design the ideal way to make the sheet metal molds you want.
Sheet metal stamping design: the cold technique
Once the sheet metal stamping design has been agreed, we make the molds at Minifaber using the cold forming technique.
We use this type of stamping mold process because, unlike hot forming, it allows you to obtain results with more precise finishes, more quickly.
All cold forming steps, from the virtual design of custom-made molds to the actual metal forming, are carried out in-house, to guarantee maximum control over the timing and quality of the final product.
Custom sheet metal stamping design
One of the strengths of Minifaber is certainly its flexibility in always wanting to meet specific customer requests. In relying on Minifaber, the customer knows that s/he will be guaranteed the maximum degree of customization in sheet metal stamping design.
The customer takes part in the design phase, interacting in person with our Engineering Department.
Precisely because of this flexibility, Minifaber is also able to design sheet metal molds for the production of fully assembled or semi-finished products, according to the customer's needs.
Minifaber molds
In particular, we specialize in the design and manufacture of the following sheet metal molds:
- Shooting molds, used to produce small quantities of components.
- Progressive molds, ideal for producing large quantities of components and at a high pace. They can create a finished product in a sequence of steps with a single mold and are thus able to achieve the best results in terms of quality, production speed and cost savings.
- Transfer molds, to create a finished product in a sequence of steps on a series of transfer connected molds. Compared to progressive molds, they provide higher processing freedom and work at a lower pace
- Deep-drawing molds, used to manufacture square shaped, hollow, cylindrical, cup-shaped or other various shaped metallic parts and finished products. Required in every industry, out deep-drawing molds guarantee the maximum precision and efficiency over time.
- Block molds, used for the production of very critical parts or with particular dimensional requirements.
In order to achieve all this, Minifaber uses a rich and state of the art fleet of machines, constantly updated and enriched by important investments that keep the company at the top of innovation, and a very high level of computerization.
So why limit a design to paper, when it is possible to shape it thanks to Minifaber’s expertise?