Breadcrumb
Mig welding and safety: how to avoid unpleasant accidents
Mig as well as tig and laser welding are essential processes in sheet metal cold moulding. Once laser cut and bent, many components are welded together to create complex parts, ready to be introduced on the market. If, on the one hand, welding is thus essential, on the other, it is a very delicate and dangerous process that can cause work accidents. Here are the solutions adopted by Minifaber to provide accurate but above all safe welding!
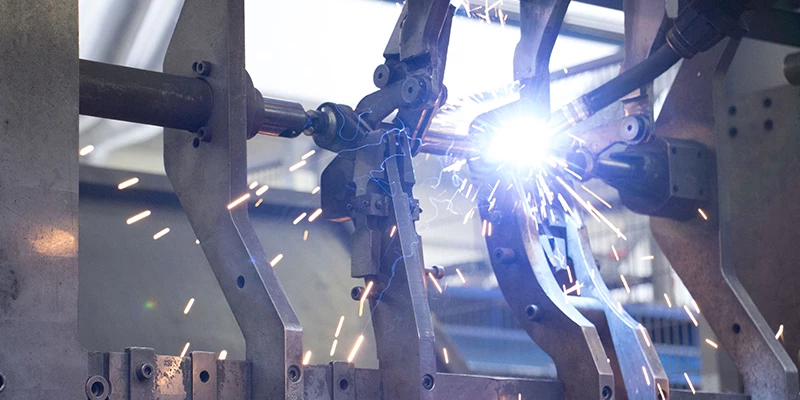
Workplace safety
Minifaber is attentive to its employees' health and safety at the workplace and, for this reason, the safety rules set by current regulations are adopted in all its departments. Specifically, production departments are not accessible to unauthorised personnel and employees must enter equipped with personal protection equipment such as safety shoes, work goggles and helmets. Furthermore, on the structural level, departments are equipped with an emergency evacuation system as well as protection devices on machinery and non-slip solutions on floors where necessary.
Mig welding: safety devices for employees
As for mig welding, the single machines are equipped with protection systems and emergency stop buttons. Mig and tig welders must also wear gloves and helmets to protect hands, arms, the face and eyes against shards that may detach during the work process.
Robotic welding systems for maximum safety
To further limit risks during mig and tig welding, Minifaber has also adopted robotic welding systems and, specifically, 1 robotic laser welding system and 3 anthropomorphic robots for mig/tig welding that prevent direct contact between the worker and the welding process. In fact, these robots are numerically controlled and department workers must manually activate them but from a due distance from the work area, reducing burn and welding injury risks to practically zero. Thus, work is more streamline, continuous and, above all, safer with robotic welding systems!